ICE Panels: Challenges of New Building Materials and Codes
- Katelyn Sebastian
- Sep 21, 2021
- 5 min read
Updated: Mar 31
Note: this post was originally published to Kilo Lima Code Community . Check out this engaging community here.

ICE Panels
Insulated Composite Envelope (ICE) panels are comprised of two layers of light gauge steel studs inset in Expanded Polystyrene Insulation (EPS). The studs are arranged on each exterior face of the panel and work integrally with the insulation to create a structural panel that may be used for roof, floor, exterior wall, or foundation wall construction.
ICE panels do not fall within the prescriptive structural design methods of Part 9 – “Housing and Small Buildings” of the National Building Code (NBC). Therefore, ICE panels must be designed in accordance with Part 4 – “Structural Design” of the NBC. As a result, each project using ICE panels requires the involvement of a structural engineer to design and stamp the ICE panel component. This means that the structural capacity of each ICE panel and connection must be analyzed and verified or modified to support the calculated design loads.
One of the greatest assets of ICE panels is their energy efficiency. Due to the size and orientation of the studs, there is no thermal bridge. This allows for a much higher insulating value than many other common construction assemblies.
Another asset of ICE panels is the speed of construction. The panels are modelled, designed, and fabricated at Greenstone’s plant, and then shipped to site. The panels show up on site pre-fabricated, of a size that is easy to work with, and with shop drawings identifying the exact install location of each labelled panel. There’s no curing time, and the approach to construction has already been determined and laid out for the contractor.
Unbeknownst to many, the technology and the concept of ICE panels have been around for multiple decades. However, the refinement of the product and the introduction of the product to mainstream construction and especially residential construction is a much shorter history. There have been both benefits and challenges to this product because of building codes.
Benefits of Building Codes and Energy Efficiency
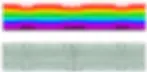
The 2015 edition of the National Building Code of Canada (NBC) introduced a new section in Part 9 – “Housing and Small Buildings”, identified as Section 9.36 – “Energy Efficiency”. The intent of the section was to create minimum standards for energy efficiency of new construction by considering the building assemblies used and how they are constructed, as well as the efficiency of HVAC and water heating systems.
Several provinces were slow to adopt this portion of the Code – Saskatchewan even delayed adoption of Section 9.36 by a full year after it had adopted the remainder of the 2015 edition. However, with that adoption came an opportunity for builders and owners to reconsider building material selection in order to meet new energy efficiency requirements.
The thermal resistance of ICE panels may be calculated following the general guidance in the Notes to the Code in A-9.36.2.4(1) for steel-frame assemblies. This method is not specifically intended to consider two layers of steel studs, and therefore requires some level of manipulation. However, there are modelling results available from the manufacturer that may be used to support accuracy of the calculated method.
Alternatively, designers may opt to bypass the prescriptive approach and use the modelling approach. Within the modelling approach, there is an opportunity to reduce construction cost by trading off ICE panel assemblies to other assemblies or ICE panel assemblies to mechanical systems.
The National Energy Code for Buildings (NECB) offers similar support and benefits for the use of ICE panels. The benefit in modelling buildings using ICE panels is even greater through NECB since trade-offs may also apply to electrical systems and allowable area of fenestrations.
Challenges of Building Codes and Energy Efficiency
The prescriptive path approach for energy efficiency of the building envelope of buildings using ICE panels is more complex than some alternate building materials. As a relatively new material to the construction industry, designers may even encounter push-back from Authorities Having Jurisdiction, especially through Part 9. As a result, designers may be requested to provide supporting documentation or even their calculations. This may be seen as a challenge to the use of the ICE panels. However, this challenge does reinforce the importance of owners and contractors to seek out knowledgeable designers for their projects, and for designers to commit to continued education.
Challenges of Building Codes and Structural Design
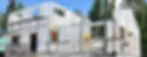
As noted previously, ICE panels are not addressed in Part 9 of the NBC and therefore must be designed through Part 4 of the NBC. This is not an approach that many owners, builders, or designers are accustomed to for housing and small buildings. While this is a challenge, it also allows for efficacy of the design, because each panel has been specifically designed for the design load applied to it.
Further, whereas the construction industry is highly familiar with floors and roofs being identified as designed by the supplier, the industry is not as familiar with seeing walls identified as designed by the supplier. An added level of coordination may be required to ensure that all shop drawings are coordinated with each other and with the permit drawings. Again, this reinforces the importance of a knowledgeable designer who has been contracted to provide full services.
Benefits of Building Codes and Structural Design
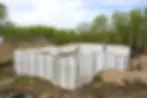
For housing and small buildings, the typical approach for implementing ICE panels to a project is similar to the approach used for engineered trusses.
A majority of housing and small buildings constructed in Canada now rely on the efficacy of engineered wood trusses for their floor and roof structures. During the design process, sufficient information is provided on the drawings for completion of the truss design. In addition, information such as the direction, shape, and spacing of the trusses are identified for coordination and permitting purposes, but the design is identified as “by supplier.” A separate package of truss shop drawings are designed and stamped by the supplier. The truss package may or may not be required by the Authority Having Jurisdiction as part of the permit application.
Similar to engineered trusses, ICE panels are designed and stamped as shop drawings, separate from the general permit drawings.
In Summary
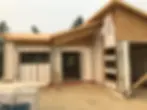
There are often Building Code challenges encountered by the introduction of new building materials to the market. However, the creation of new building materials is generally always driven by a need to solve a problem – faster construction, reduced construction costs, improved energy efficiency, etc.
For any new building material, the path forward must be through education:
Education of owners, designers, contractors, and building officials on the building material,
Sharing of best practices for approaching design, construction, and permitting,
Procurement and availability of test data, and
Determine if or how the building material might be better incorporated into future building codes.
For more information on ICE panels, visit http://www.gsbp.ca